TOP RESEARCH Subject of Research
Subject of research
Kasai Laboratory started to its research activities from April, 2004. At present, its total members are 11, ie, 7 staffs (4 are of casual staffs), 4 students. Its researches are sorted into the following three areas:
- Improvement of the efficiencies and reduction of the environmental loads in the high temperature processes with complex reactions, eg, recycling of metal scraps, waste incineration/treatment and base metal productions
- Efficient remediation/removal of POPs (Persistent Organic Pollutants) containing in the soils, bottom sediments of river, harbors and canals, and also industrial waste water. Volume reduction of sludge formed during the treatment of organic waste water and enhanced recoveries of energy & mineral resources from the sludge.
- Development of new processing method to create functional materials, eg, coating of metals and porous metals.
 |
Development of the Composite of Carbonaceous Materials and Iron Ores for Reduction of CO2 Emission from Ironmaking Process |
Due to rapid increase of world steel production, steel industry is facing two difficult tusks to solve simultaneously.
One is the reduction of CO2 emissions and another is the effective use of low-grade iron ore resources which contains relatively large concentration of combined water.
Lowering the reduction temperature of iron oxide using a composite consisted of iron ores and carbonaceous materials are promising ways to solve the former problem.
The latter is mainly concerning to the Australian ores, i.e., Pisolite and Marra Mammba ores. In this study, effects of particle size and the concentration of combined water of different iron ores on the reduction and gasification behaviors of the composite were examined.
The coal/ore composite sample was heated up to 1573 K with the heating rate of 0.33 K/s under Ar gas flow.
The formed gases during the experiment were analyzed and the results were used to the calculation of the changes in the reduction and gasification degrees.
The peak of gasification rate for the composite using Pisolite and Marra Mammba ores was obtained at approximately 1173 K, which was significantly lower from that for hematite ore.
Below 1373 K, the gasification degree increased with increasing the combined water concentration of the ore as shown in Fig. 1.
It appears that the gasification reaction was accelerated by the catalytic effect of metallic iron formed by the reduction observed at 1193 K in the cases for ores containing higher combined water.
Accordingly, the higher reduction degree was obtained at below 1373 K. At higher temperature above 1473 K, however, the reduction degree of the composite of hematite ore became higher.
This is because the reduction of the composite of ores with high combined water retarded at higher temperatures.
Top of the page
 |
Improvements of the Efficiency and Environmental Friendliness of Agglomeration Process of Iron Ores |
A new agglomeration (sintering) process iron ores having sufficient flexibility for future changes of the iron ores has been developed.
Especially Marra Mammba and “high phosphorus brockman”, which are fine Australian iron ores containing goethite and phosphorous, are main targets.
Because they have remarkably large deposit but is regarded as ores hard to use to the sintering process.
A new agglomeration process named “MEBIOS (Mosaic Embedding Iron Ore Sintering process)”, which aims an efficient utilization of low-grade ores ensuring high productivity of sinter by separating the raw materials into a conventional mixture and green pellets of larger size, has been proposed and has been examined in an industry-university joint-research project, from 2005 to 2009.
Our laboratory developed two-dimensional (2D) and three-dimensional (3D) simulation models in order to analyze the heat transfer phenomena in the sintering bed in detail.
The models were built on the basis of the concept of the multiply shared space (MUSES) method, which can be easily applied to flows and heat and mass transfers occurring in a porous material.
The time variations of temperature at the center of the pellets distributed in lattice and staggered alignments in the sintering bed of the MEBIOS process were calculated by both the 2D and 3D simulations and the results shows that they were similar to each other.
Since the calculation time for the 2D simulation was significantly shorter than that for the 3D simulation, it is suggested that the former should be first tried under different conditions, and then some selected calculations should be performed using the 3D model.
The calculated results show that the sintering process cannot continue, when the pellets were placed as the staggered alignment with 30 mm distance between pellet centers due to lower gas velocity around them.
Top of the page
 |
Increase in the Process Efficiency of ISP Sintering |
ISP (Imperial Smelting process) is an important dry process for zinc production, which can produce lead together with zinc.
Therefore, it plays an important role to construct a heavy metal recycling system of EAF (Electric Arc Furnace) dust for steel making and secondary fly ashes of the gasification-melting furnaces for solid waste and the melting furnaces for incineration ash.
The process needs agglomeration of fine raw materials before charging them into the smelting reduction furnace.
The agglomeration is made by the Dwight-Lloyd sintering machine similar to the iron ore sintering (but it is an up-draft type).
Its main energy source is the oxidation heat of sulfur contained in the sulfide ores. Generally, although the production rate of this type of process is high, the ISP sintering cannot reach to the sufficient level due to lower product yield led by extremely fine raw materials.
However, it means that if we can increase the product yield, ie, decrease the return ore ratio, it will be possible to increase the amount of recycle dusts used as raw materials.
In this study, ways to increase in the product yield are examined through the optimizations of granulation process of raw materials and/or the structure of prepared granules.
For example, effects of the pretreatment of oxide dusts, size distribution of return ore and application of separated-granulation are fundamentally evaluated.
Top of the page
 |
Development of the Production Process for Functional Formed Steel by Utilizing Reduction of Iron Oxide |
Major application of foamed metals is energy absorber which composed with high strength materials is large.
Strengthening of aluminum foams due to its alloying has been advanced.
Steel is lower law material cost, higher strength and better weldability to other steel structural materials than aluminum based materials.
If iron based foam materials with high porosity can be manufactured, like aluminum foam, it is expected to be used as weight saving and high-functional materials in such applications as also transport machines and structural parts.
However, no foaming agent was development for manufacturing steel foam though most famous foaming agent for manufacturing aluminum foam is titanium hydride.
Our group focused on the gas of CO and CO2 generated by the reduction of iron oxide as foaming agent. Development of the production process for steel foams using electrolytic iron, hematite and graphite powders are carried out.
Figure 4 shows a schematic drawing of foaming model in this study.
Steel foam is manufactured by rapid heating of a green compact of the mixed powder as following three steps. The first step is the heating of the compact beyond eutectic temperature and the melt of iron by reacting with graphite powder.
The second step is the generation of foaming gas by the abrupt proceeding the reduction of iron oxide due to the connection between iron oxide and carbon in the molten pig iron.
Subsequently, molten pig iron is foamed. Porosity, pore shape and distribution, microstructure and mechanical properties of the foamed iron and steel are evaluated.
Top of the page
 |
Treatment & Recycle Use of Asbestos Wastes Combined with Incineration Ash with High Efficiency and Reliability |
Asbestos has been widely used in the industries as building materials, electrical products, automobile components and so on, since it posses various beneficial properties, eg, heat and chemical resistances and insulation properties.
The total amount of imported asbestos between 1925 and 2005 were huge, about ten million tones.
They will become to be wastes together with other materials like mortar and the annual generation of the asbestos wastes will be more than one million for next 30 years.
In order to establish a safe and secure process of the melting treatment for asbestos wastes, the properties of asbestos and asbestos waste samples are first studied in detail.
Further, the knowledge for the slag formation in the metallurgical processes are applied to the development of such process.
The melting behaviors of asbestos samples were examined by TG-DTA and confocal scanning laser microscopy for high temperature observation.
It is especially focused on the softening and melting temperatures and melt-down behaviors of chrysotile, crocidolite, amosite and the asbestos wastes containing such asbestos.
This study is supported by the Ministry of Environment, Japan and conducted as a joint-research with the Mogami Clean Center in Yamagata Prefecture.
Top of the page
 |
Development of UMCA (Ultrasonic Mechanical Coating & Armouring) process for Coating Treatment of Metallic Surfaces |
A new ultrasonic-based dry mechanical method for armouring or coating metallic surfaces with other metal or ceramic materials have been proposed by this laboratory.
In the method, hard balls (of metals or ceramics such as stainless steel or ZrO2) are put into a bowl-shaped resonant chamber which is fixed beneath the substrate surface to be coated and metal or ceramic powder are precoated in ethanol suspension with the substrate surface.
The chamber is set into high frequency vibration (20,000 Hz) by an ultrasonic transducer attached to the chamber bottom.
This initiates a chaotic motion and collision of the balls and powder particles results in grinding the particles, and hammering them into the metallic surface.
Experimental examinations dealing with many kinds of combinations of substrate and powder, such as Al/Ti, SUS/LaPO4 and (Al,Ti,SUS)/TiN were performed in order to give functions of high temperature oxidation and wear resistances on the substrate surfaces.
The results revealed that the coating efficiency is dependent on several parameters including the ball number, particle size and ball-to-particle weight ratio.
Coatings can be formed in a short time at room temperature under ambient atmosphere by repeated substrate-to-ball collisions of coldwelded powder particles.
On the whole, the method was found to offer a number of attractive features that may make it useful for many practical applications.
This project is one of the joint researches with the Institute of Scientific and Industrial Research (ISIR) of Osaka University in the Materials Science & Technology Research Center for Industrial Creation (MSTeC).d to offer a number of attractive features that may make it useful for many practical applications.
This project is one of the joint researches with the Institute of Scientific and Industrial Research (ISIR) of Osaka University in the Materials Science & Technology Research Center for Industrial Creation (MSTeC).
Top of the page
 |
Acceleration of Sonochemical Degradation of Persistent Organic Pollutants (POPs) in Water and Sediment |
Persistent organic pollutants (POPs) are very difficult to degrade when present in the environment and finally accumulate in the human body.
Therefore, it is essential to develop efficient technologies for removal of POPs from polluted waters and sediments.
Our laboratory has already succeeded to increase considerably the efficiency of ultrasonically assisted degradation of model POPs, 4-chlorophenol and 1,2-dichrolobenzene, by the combination with Fenton reaction, which generates OH radicals from the reaction between Fe2+ ion and H2O2 (Fe2++ H2O2→Fe3++ OH +OH-) using iron powder and mill scale particles as Fe2+ ions source.
Now we attempt to evaluate the potential of hexachloro- benzene (HCB; a POP) removal by using ultrasonic irradiation and its combination with other advanced chemical oxidation processes (AOPs) and surfactant addition.
The average removal ratios for ultrasonic irradiation alone and ultrasonic in combination with UV light irradiation were almost identical at 40%, and the efficiency could be improved to about 49% by combination with photocatalysis or surfactant addition.
The dual-frequency ultrasonic irradiation showed the highest HCB removal ratio (57%).
Top of the page
 |
Development of the dispersed-type sonophotocatalytic process using piezoelectric effect excited by ultrasonic resonance |
In order to apply sonophotocatalysis (SP), which is the combination of sonolysis and photocatalysis, in the actual waste water treatment processes, we propose that plural UV-LEDs are used instead of a mercury lamp and they are dispersed to promote photocatalytic reaction in the whole of the reactor.
The innovative idea for supplying electricity to dispersing UV-LEDs can be explained as follows: Ultrasound is irradiated to the light emitting device composed of a piezoelectric element and UV-LEDs, and piezoelectric effect is excited by ultrasonic resonance of the piezoelectric element to lead light emission of the UV-LEDs.
It is not necessary to supply electric power directly but light emitting of the dispersing UV-LEDs is possible.
The sonophotocatalytic process based on this concept is called the 'dispersed-type' sonophotocatalysis.
The light emitting device composed of a piezoelectric element and 8 UV-LEDs was developed and used for sonophotocatalytic degradation experiments of methylene blue in aqueous solution.
The sonolytic, photocatalytic and fixed-type sonophotocatalytic treatments were also carried out to compare. The results showed that the degradation rate constant was highest in the case of dispersed-SP due to the promotion of photocatalytic degradation in the whole sample.
Now using the dispersed-type sonophotocatalysis, the degradation of actual organic pollutant such as dichlorobenzene and the application as a pretreatment process for volume reduction of organic sludges and resource recovery from them are also examined.
Top of the page
 |
Emission and Decomposition Behavior of HCB (Hexa-Chlorinated Benzene) from EAF (Electric Arc Furnace) Dust |
HCB (Hexa-Chlorinated Benzene) has been specified in the Stockholm Invention as an unintentionally formed compounds of POPs (Persistent Organic Pollutants) together with dioxins (PCDD/Fs) and PCBs which have potentials to affect to the human health and the surrounding ecosystems.
Therefore, its emission inventory has to be established and further the reduction plan to reduce its emission has to be drawn up.
The steelmaking process by EAF emits a certain amount of HCB and the project to understand its formation mechanism has started recently.
In this study, the formation and decomposition behaviors of HCB during the treatment process of the outlet gas from EAF, in the course of during the gas cooling and dust collection processes, will be investigated.
At present, the formation of HCB from the EAF dust in the low temperature between 50 and 400oC is being experimentally examined.
Top of the page
|
 |
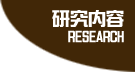
subject of research
Lab. tour
|