Research
  Our laboratory focusses on developing and designing eco-friendly materials and processes using physical fields, and on elucidating the effects of these fields on the reaction kinetics, transport and interface phenomena.
Examples of such fields include ultrasonic and electromagnetic fields, microwaves and plasma.
  Some advantages of this approach are : (1) minimization of chemical waste, (2) reduction of process temperature, (3) improvement of material recyclability.
  In this research, in order to achieve full recycling of alluminum scrap, the new type of inoculants which would be capable of refining or modifying the intermetallic compounds was investigated. A possible approach was showed below. Inoculants could be synthesized by means of ball milling. Then, the synthesized particles of inoculant were added into molten aluminum to produce a master alloy.
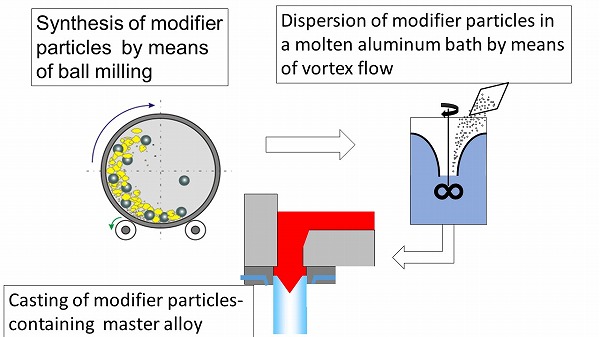
Modification treatment of aluminium scrap
  The aim of this research is to establish technological principles of a novel ultrasonically-assisted process UMCA (Ultrasonic Mechanical Coating and Armouring) for fabrication of nanostructured coatings or composite layers on metal or ceramic substrates.
The basic principle of the process is that a layer of powders, predeposited on the substrates, is subjected to treatment with high-energy impact shots accelerated by high intense ultrasonic vibrations.
The process provides the following treatments in one operation step: 1) grinding of metal or/and ceramic powders, 2) transferring of the powder particles onto the surface of metal or ceramic substrate, 3) severe deforming and hammering of the particles into substrate surface layer, 4) cold hardening and cold welding of the particles onto the substrate.
The process can be performed at room temperature and atmospheric pressure, and offers a great flexibility in choosing materials for substrate and coating.
  Up to now, it has been shown that the process is capable of producing high-dense and high-adhesive layers of TiN, LaPO4, SiC, Ti of several microns in thickeness on metal (Al, Ti, steel) or ceramic (Al2O3) substrates. At the present stage, we mainly focus on elucidating mechanisms and phenomena related to the treatment process. Among these are cold welding, diffusion bonding, severe plastic deformation, microforging and plastic flow.
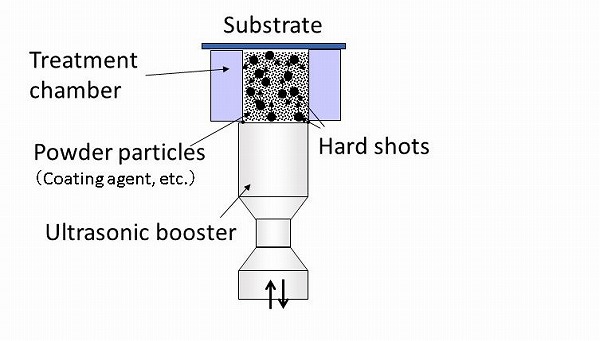
Schmatic image of UMCA process
  Some advantages of this approach are : (1) minimization of chemical waste, (2) reduction of process temperature, (3) improvement of material recyclability.
Impact treatment
1. Modification treatment of intermetallic compound to improve recyclability of aluminium scrap
2. Development of novel environmentally-friendly process for mechanical coating and surface modification
  Producing aluminum from scrap could save 97% energy compared with it from bauxite. However, at present, recycling ratio of wrought alloys is under 25%.
One resaon for that is the impurity in the aluminum alloy, such as Fe, Cr, Ni and Ti, which result in the formation of coarse intermetallic compounds.2. Development of novel environmentally-friendly process for mechanical coating and surface modification
  In this research, in order to achieve full recycling of alluminum scrap, the new type of inoculants which would be capable of refining or modifying the intermetallic compounds was investigated. A possible approach was showed below. Inoculants could be synthesized by means of ball milling. Then, the synthesized particles of inoculant were added into molten aluminum to produce a master alloy.
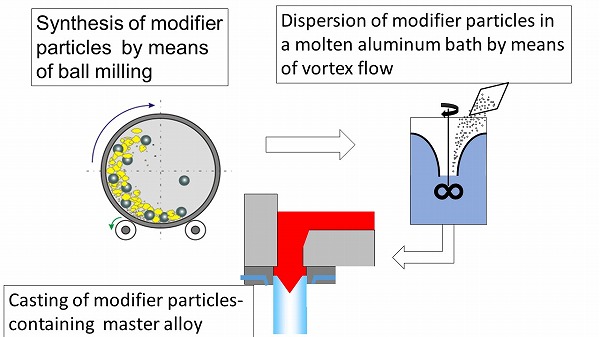
Modification treatment of aluminium scrap
  Up to now, it has been shown that the process is capable of producing high-dense and high-adhesive layers of TiN, LaPO4, SiC, Ti of several microns in thickeness on metal (Al, Ti, steel) or ceramic (Al2O3) substrates. At the present stage, we mainly focus on elucidating mechanisms and phenomena related to the treatment process. Among these are cold welding, diffusion bonding, severe plastic deformation, microforging and plastic flow.
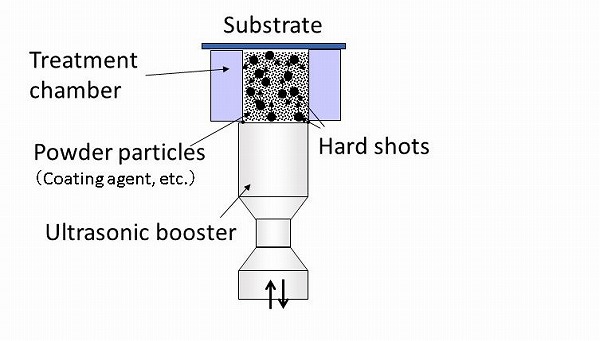
Schmatic image of UMCA process